N2 Booster Pumps vs. N2 Booster Compressors: The Differences
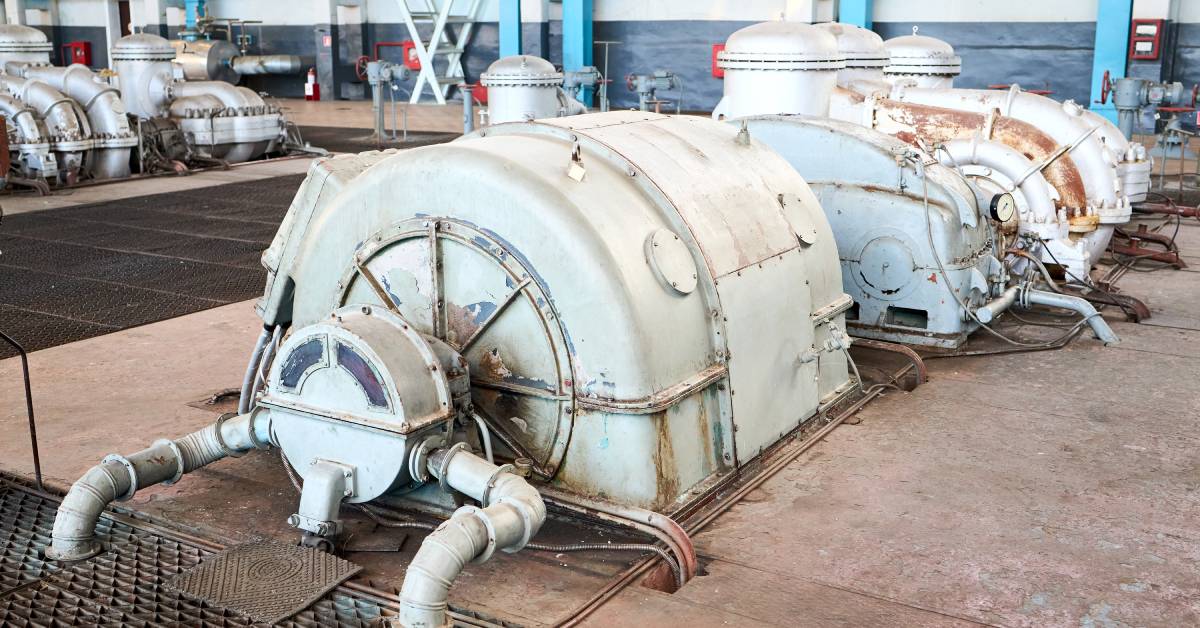
Many industries require a means to boost the pressure of nitrogen gas, commonly referred to as N2. This is because raw N2 is typically produced at a lower pressure than what is needed for various industrial processes. Two common options that meet this demand are N2 booster pumps and N2 booster compressors. While they both serve the same purpose, there are differences between these two types of equipment that are important to understand so that you can select the most suitable option for a specific application.
What Are N2 Booster Pumps?
N2 booster pumps are mechanical devices that use a piston or diaphragm to increase the pressure of nitrogen gas. They work by drawing in low-pressure N2 gas and compressing it to higher pressure before releasing it back into the system. These pumps can boost pressures as high as 36,000 psi and are commonly used at point of use in industrial applications such as:
- Pressure Testing: Piping or Components for leakage.
- Gas Injection: Chemical process or plastic forming
- Gas Scavenging: Collecting gas from partially used cylinder/bottles and transferring to receivers.
- Life support: Gas transfer & Charging e.g. oxygen, helium, breathing air, firefighting equipment, Hazmat equipment
- Compressing: Natural gas (CNG ) Boosting for vehicle re-fueling
What Are N2 Booster Compressors?
N2 booster compressors are more complex and use a multi-stage process to boost the pressure of N2 gas. They also work by drawing in low-pressure N2 gas, but instead of using a piston or diaphragm, they use impellers or screws to compress the gas through multiple stages until it reaches the desired pressure. These compressors can achieve higher pressures than pumps, up to 60,000 psi or more, and are better suited for larger applications that require a high flow rate. Transmission Lines: Bulk gas transfer.
What’s the Difference Between N2 Booster Pumps and Compressors?
While N2 booster pumps and compressors both serve the same purpose of increasing nitrogen gas pressure, there are some differences between them that set them apart.
- Infinitely Variable Output: Pneumatic driven pumps output can be controlled via a variable drive pneumatic/air flow. While a fixed ratio between the inlet & outlet pressure is maintained.
- Simple Controls: No Electricity, No heat or possibility of flames
- Technology: N2 booster pumps use positive displacement technology, while compressors use dynamic compression. This means that N2 booster pumps physically move gas molecules to increase pressure, whereas compressors rely on high-speed rotating impellers or blades to create pressure.
- Energy efficiency: N2 booster pumps are generally more energy-efficient than compressors because they don’t rely on high-speed rotating components. The clearances between rotating components in compressors. allow leakage between the parts resulting in lower efficiency. N2 Booster closes clearances and seals to minimize energy consumption and operating costs.
- Maintenance: In terms of maintenance, N2 booster pumps have simpler designs and fewer moving parts compared to compressors, making them easier to maintain and repair. For pumps, maintenance usually involves replacing worn-out seals or gaskets, while compressors may require more complex repairs and overhauls.
- Cost: N2 booster pumps are typically less expensive to purchase and operate than compressors due to their simpler design, lower energy consumption, and easier maintenance requirements.
- Size and portability: Because of their simpler design and smaller size, N2 booster pumps are more portable and easier to move around compared to compressors. Compressors are larger in size and often require permanent installation.
- Pressure range: As mentioned earlier, N2 booster pumps can reach a maximum pressure of 36,000 psi, while compressors can achieve pressures up to 60,000 psi or more. This makes compressors better suited for larger applications that require high-pressure outputs.
- Flow rate: N2 booster pumps have a lower flow rate compared to compressors due to their positive displacement technology. Compressors have a higher flow rate because they use multiple stages to compress gas.
Basically, Air Driven Booster pumps are smaller, simpler, and more cost-effective for a wide range-pressure applications, while compressors are better suited for larger applications requiring higher pressures.
Which One Is Better for My Application?
Should you use an N2 booster pump or a compressor for your application? Ask yourself the following questions. Your answers will help you determine which option is better for your use case.
What Application Are You Using It For?
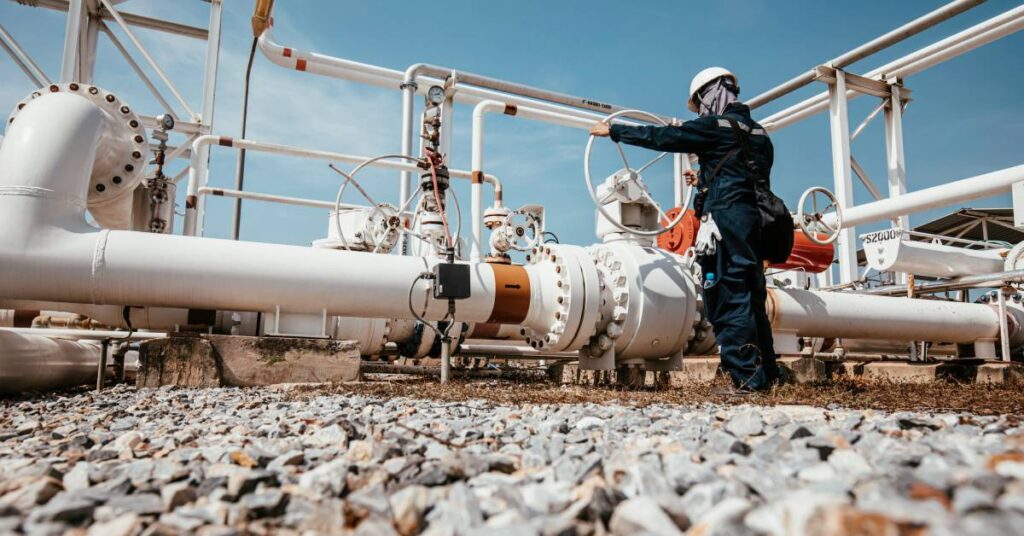
N2 booster pumps are most suitable for applications that require moderate pressure increases. Examples include machine tool clamping, where you need moderate pressure to hold workpieces in place, and gas-assisted injection molding, where you use N2 as a propellant for plastic parts. Compressors are better suited for applications that require higher pressures, such as gas turbine starting, oil and gas pipeline testing, and chemical processing.
How Much Time and Resources Can You Allocate for Maintenance?
Do you have the time and resources to perform regular maintenance and repairs on your equipment? If not, an N2 booster pump may be a better option due to its simpler design and easier maintenance requirements. Compressors may require more frequent and complex maintenance, which can be time-consuming and costly.
What Is Your Budget?
How much are you willing to spend on equipment and operating costs? N2 booster pumps tend to be more affordable upfront and have lower operating costs compared to compressors. But if your application requires a higher-pressure range, you may need a compressor despite the higher initial cost.
What Space Constraints Do You Have?
Consider the available space for your equipment. N2 booster pumps are typically smaller and more compact, making them suitable for applications with limited space. Compressors may require a larger footprint due to their multiple stages and rotating components.
What Pressure Range Do You Need?
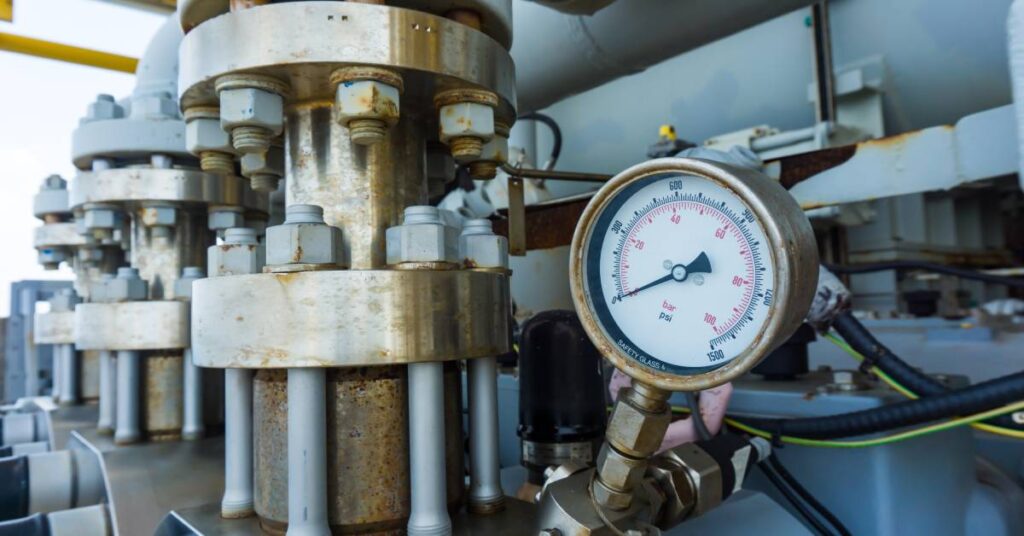
Consider the required pressure range for your application. If you need to boost nitrogen gas up to 35,000 psi, both options will work. But if you require pressures above 35,000 psi, you may need to use a compressor.
What Flow Rate Do You Need?
If your application requires very high flow rates, a compressor may be the better option due to its multi-stage compression process. If you only need low to moderate flow rates, you can use a N2 booster pump.
If you need to increase the pressure of nitrogen gas, both N2 booster pumps and compressors can help with the task. But instead of picking one for the job at random, consider what sets each option apart and which one suits your application better. While they do serve the same purpose, their differences can affect how well they perform in each situation. You don’t want to purchase a booster pump only to realize it can’t handle the required pressure range, and you don’t want to invest in a compressor when a pump would have been more cost-effective and easier to maintain.
At SCI Sharp Controls, we sell Air Driven Gas Booster Pumps for a variety of gas applications; N2, H2, O2 industrial and O2 Breathing, Halon, Sour gas and refrigerants from top manufacturers like Hydraulics International Inc. And HiP (High Pressure Equipment aka: Sprague)
These are fixed ratio, positive displacement pumps to meet various pressure and flow requirements, as well as a variety of sealing and materials of construction depending on what your application requires. If you’re not sure which one is best for your application or materials compatibility, our team can help you select the right options based on your requirements and budget. Contact us today for more information or to request a quote.